Table Of Content

Hydraulic systems are commonly used in applications that require significant force, such as lifting heavy objects or operating in rugged environments. They offer excellent control over force and speed, making them suitable for tasks that demand both power and precision. Hydraulic actuators use pressurized fluids to generate force and motion in robot arms. These systems are known for their high power and ability to handle heavy payloads. Inverse kinematics is particularly useful when a desired position or orientation of the end effector needs to be achieved. It allows engineers to calculate the joint angles needed to achieve a particular configuration, enabling precise control over the arm’s movements.
Share this news article on:
By building your own robotic arm, you will gain a better understanding of how these technologies work together. You will also have a lot of fun watching your robot arm move and interact with its environment. First, you’ll need to connect the controller to the base of the robotic arm. Robotics is a growing field with many applications in both industry and research. In this tutorial, we will show you how to build a robotic arm from scratch using easily- available materials.
EEZYbotARM MK3: The Second Base
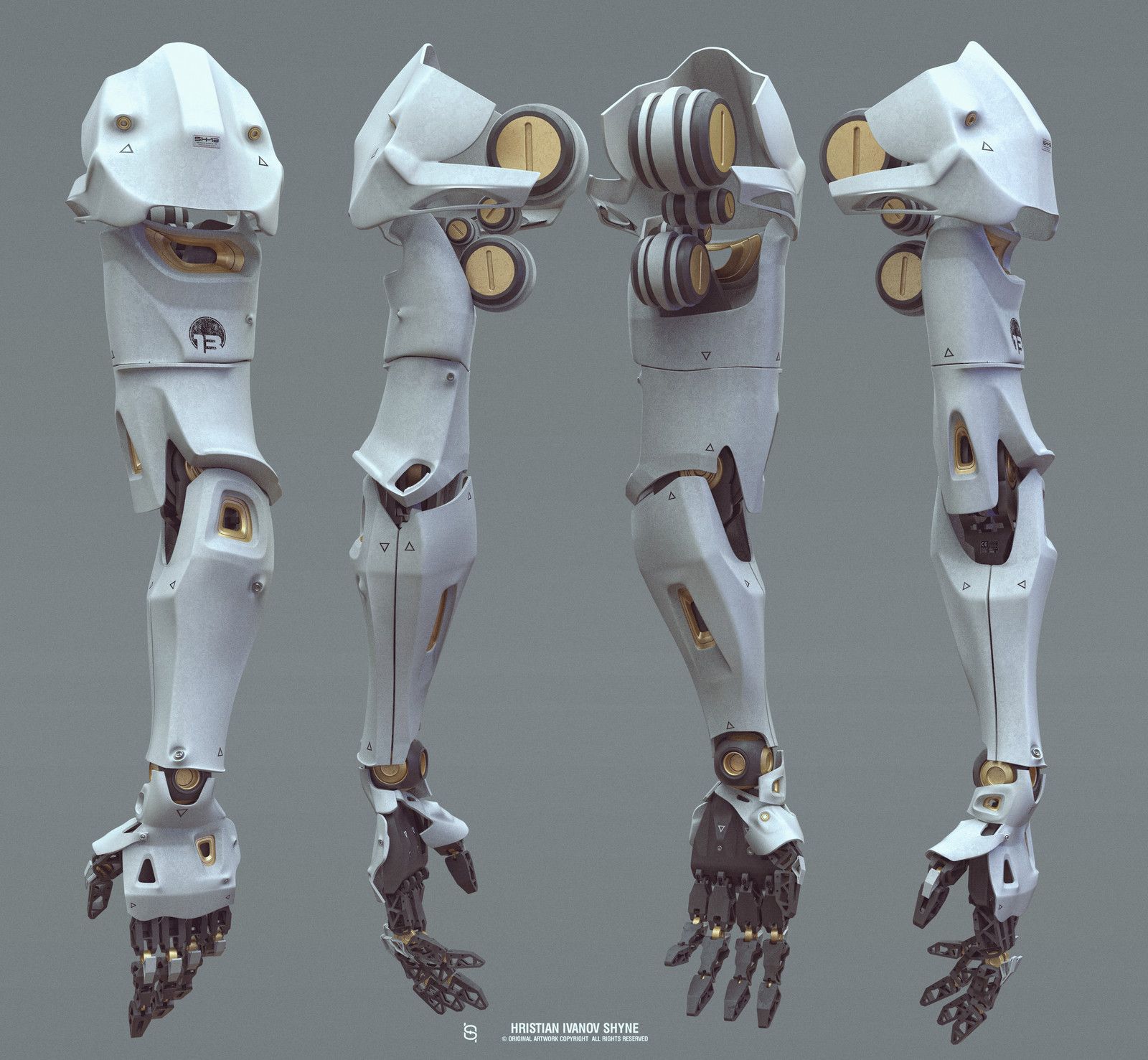
The design of delta arms allows them to perform these tasks with remarkable speed and accuracy. Cameras and image processing algorithms allow the arm to perceive and understand its surroundings, enabling it to locate and manipulate objects with precision. After all the adjusting was complete, I could determine the robotic arm’s limitations on movement and load. The time of execution for lifting the forearm is 7 seconds, extending the arm took 10 seconds and closing the claw took 4 seconds.
Custom robots in a matter of minutes
By understanding the intricacies of robot arm design, we can unlock a world of possibilities and harness the full potential of these mechanical wonders. DC motors are commonly used when continuous rotation is required, such as in articulated and SCARA arms. These arms are commonly used in applications that require a wide range of motion, such as painting, welding, or inspection tasks. Their ability to reach objects from various angles and positions makes them highly versatile and suitable for complex tasks. There are several types of joints commonly used in robot arms, including revolute joints, prismatic joints, and cylindrical joints.
Amazing Coding Robots for 2024
By altering the connection lengths and permitted degrees of freedom for the mechanism, the work volume produced in this way specifies the usable space for the robot. The end effector, also known as end-of-arm tooling, is a gadget or tool that is attached to the end of a robotic arm, and which interacts with the robot’s assigned task. The design of an end effector, as well as the hardware and software that operate it, is dependent on the robot’s task or application. The robotic arm's wrist connects the forearm and the end effector and ensures the end effector’s precision. However, the wrist's rotation can be limited because the robot's base itself rotates. The forearm determines the robot's range and moves more compared to the other components.
The delta robot is a great choice for high-speed and lightweight tasks. The mechanical design may be limited to 6 DoF as it permits all necessary movements. In Robotic Arm Design of serial and parallel manipulator systems, the end effector is positioned with five degrees of freedom, consisting of three translational DoF and two for orientation. A direct relation can thus be obtained between actuator position and manipulator configuration. In Robotic Arm Design, the degree of freedom (DoF) of a robot is determined using the total number of freedom of the rigid body minus the number of constraint on it’s motion.
Living woodlice and marine mollusks act as "grippers" for robot hands in a new study - Interesting Engineering
Living woodlice and marine mollusks act as "grippers" for robot hands in a new study.
Posted: Thu, 22 Jun 2023 07:00:00 GMT [source]
Types of Robotic Arms

The two threaded rods are rotated by a motor attached to a bracket on the base on which is the model’s first arm connector is located. The threaded rod is connected by the two nuts, the first being attached to the component that connects the motor to the rod, the second fixed by a piece fixed in the robotic arm. The rod has the ability to rotate around its axis, resulting in a linear motion. Meanwhile, on the disadvantage side, threaded rods require a complex mechanism.
Better Precision
A simplified hand that can grip and carry various things is one frequent end effector. It usually has two claws, but it can also have three, which can open and close on demand. It may also be spun on the wrist, making it simple to move materials and equipment. With the controller and programming in place, the robotic arm is ready to use.
Notable applications of Robotic Arm
However, sometimes robots can be better at certain tasks than humans—like repeating the exact same motion over and over again. This is why robotic arms like the one in Figure 1 are frequently used in factory assembly lines to perform repetitive tasks with high precision. The general-purpose nature of robotic arms allows them to be great choices for many applications regardless of industry.
Exploring 3D printing robotics is easier and cheaper than ever before, so there is no excuse not to give it a go. Having said that, it takes a lot of time and practice to become an expert. While you might not be ready to build a Terminator in your bedroom, 3D printing robotic arms is an excellent starting point for enthusiasts.
Cartesian robot arms are called after the Cartesian coordinate system and are frequently referred to as rectilinear or gantry robot arms. In essence, the widely used system of X, Y, and (less often) Z axes that we nearly always see represented on any normal graph is a result of cartesian coordinates. One of the most popular projects for hobbyists and DIY enthusiasts is building a robotic arm. A robotic arm is a great project because it is a complex system that requires the use of many different technologies.
It could be a welding interface to hold the electrodes or a hand-like gripper designed for pick and place operations in a specific area, as seen below. Based in Las Vegas, Nevada, Haddington Dynamics have developed the Mark Henry of 3D printable robot arms. Previous attempts to create a robot arm, affectionately named ‘Dexter,’ using PLA were too weak for HD’s liking. However, after one customer’s advice, and in collaboration with NASA, they began using a Markforged printer. It is compatible with the most common operating software, and photos provided on their website even feature an Xbox controller!
It implements a serial command interface with a very simple ASCII string protocol for receiving target angles from the companion computer. It also implements a PID control loop for controlling the rotation angle of the DC motor at joint 1. When programming and using them, there is an urgent need to be highly cautious as they greatly boost production speeds and precision of placement. However, this isn't the case with the cobot arms provided by Universal Robots as they have a good risk assessment.
You can also program the arm to perform certain tasks or sequences of tasks. This makes it a valuable tool for mechanics and construction companies. Depending on the input power source, servos are either AD or DC (battery operated) motors. In general, servo motors provide high torque to inertia ratio, which is achieved through an inbuilt gear system. The small and compact DC servo motors are highly popular with toys, educational robotic applications, and RC planes.
As other robotic mechanisms, robot arms are typically classified in terms of the number of degrees of freedom. Usually, the number of degrees of freedom is equal to the number of joints that move the links of the robot arm. At least six degrees of freedom are required to enable the robot hand to reach an arbitrary pose (position and orientation) in three dimensional space. Additional degrees of freedom allow to change the configuration of some link on the arm (e.g., elbow up/down), while keeping the robot hand in the same pose. Inverse kinematics is the mathematical process to calculate the configuration of an arm, typically in terms of joint angles, given a desired pose of the robot hand in three dimensional space.
These robotic arms have been used to perform a variety of tasks such as inspection of the Space Shuttle. The 2018 Mars lander InSight has a robotic arm called the IDA, it has a camera, grappler, which is used to move special instruments—Wikipedia. Figure 1 is a block diagram showing the main components of the robotic arm. The embedded controller determines the pose of the robotic arm by commanding each of the four joint motors to the desired angles.
No comments:
Post a Comment